一文(wén)讀懂樹脂結合劑
1 樹脂結合劑的化學(xué)性質(zhì)和類型
樹脂磨輪由樹脂結合劑中的磨料顆粒組成,可(kě)能(néng)含有或不含有填料(見圖1)。與燒結粘合工具相比,這種砂輪類型通常具有較低的孔隙率。
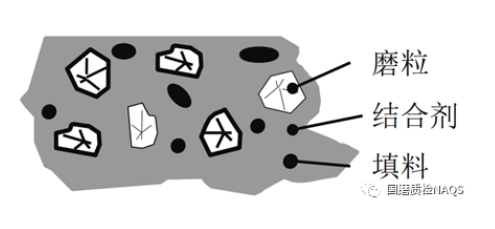
圖1 樹脂結合劑砂輪結構
樹脂是能(néng)夠硬化的粘稠液體(tǐ)。它們是聚合物(wù),即由單體(tǐ)組成的大分(fēn)子鏈。單體(tǐ)是含有C、H、O、N、Cl、S或F的元素的物(wù)質(zhì),由此合成低聚物(wù)(“樹脂”)。然後,這些低聚物(wù)在第二步中被轉化為(wèi)交聯的、不溶的聚合物(wù),這一步被稱為(wèi)固化,可(kě)能(néng)涉及到熱、催化劑、填料或壓力。
磨具樹脂結合劑由單一樹脂或樹脂組合構成,可(kě)能(néng)含有填料。樹脂本身通常是通過酯化或皂化有機化合物(wù)制造的。填料不僅有加強結合劑在韌性、耐熱性、強度和破裂安(ān)全性方面的任務(wù),而且還有支持磨削過程作(zuò)為(wèi)次要磨料的作(zuò)用(yòng)。矽酸鹽、硫化物(wù)、鹵化物(wù)增加了結合劑的強度和耐磨性,并阻止了樹脂的氧化降解。在切割輪中,樹脂結合劑還被玻璃纖維、亞麻布等體(tǐ)材料加強。
根據強度和耐溫性,樹脂結合劑可(kě)以分(fēn)為(wèi)三類:
1.1 酚醛樹脂
酚醛樹脂結合劑,特别是酚醛醛樹脂結合劑,是最常見的樹脂結合劑;這種結合劑類型的工具在傳統砂輪中占據了******的市場份額,僅次于燒結工具。最初,這種結合劑類型被稱為(wèi)酚醛塑料,因此在許多(duō)砂輪規格中保留了字母“B”。與其他(tā)樹脂相比,酚醛樹脂的價格更便宜,更容易成型。
酚醛樹脂是通過酚和醛的反應得到的。酚是芳香化合物(wù),羟基與芳香環鍵合。酚的合成通常是通過丙烯過程完成的,這是一個将丙烯(異丙苯)和空氣氧化為(wèi)丙烯過氧化物(wù)的過程,然後将丙烯過氧化物(wù)裂解為(wèi)酚和丙酮。安(ān)全性是工廠設計和操作(zuò)的關鍵因素,因為(wèi)氧化過程接近可(kě)燃極限,丙烯過氧化物(wù)是一種不穩定的物(wù)質(zhì)。
用(yòng)于砂輪結合劑生産的相關醛包括甲醛、糠醛和六甲基四胺。甲醛是一種有害化學(xué)品,當濃度超過一定程度時,可(kě)能(néng)會刺激眼睛、鼻子和喉嚨。六次甲基四胺,也稱為(wèi)烏洛托品,是酚醛樹脂結合劑中常見的硬化劑(見圖2)。基本氧化物(wù)如氧化鈣或氧化鎂是酚醛樹脂中的固化加速劑。
催化方式和酚與醛的摩爾比導緻樹脂是resole型還是novolak型。Resoles可(kě)以通過酸、堿或熱條件輕松固化;novolaks通過六甲基四胺的甲醛、固體(tǐ)resoles或其他(tā)方法固化。Resoles可(kě)以是固體(tǐ)resole、resole溶液或水性resole;novolaks可(kě)以是固體(tǐ)樹脂、novolak溶液、水性novolak分(fēn)散液和含有六甲基四胺的粉末樹脂。對于磨料工具的制造,水性resole和粉末novolak是最重要的形式。
1.2 酚醛樹脂
砂輪的酚醛樹脂結合劑包含液體(tǐ)(resole)和粉末(novolak),直接和改性酚醛樹脂,含有潤濕劑的粉末樹脂,或低熔點酚醛樹脂與粉末酚醛樹脂的組合。可(kě)以進行各種改性,如與環氧樹脂、橡膠、聚乙烯醇丁酮等的改性。此外,用(yòng)于超硬磨料的酚醛樹脂結合劑通過SiC顆粒和固體(tǐ)潤滑劑進行增強。酚醛樹脂通過聚縮反應在大約150-200°C下固化。Gardziella等人給出了用(yòng)于生産磨具的單一液體(tǐ)和樹脂粉的詳細組成。
1.3 聚酰胺和聚酰亞胺樹脂
聚酰亞胺是聚合物(wù),其分(fēn)子鏈中的一個環中含有非碳原子氮。聚酰胺-酰亞胺是同一聚合物(wù)家族的成員,含有芳香環和氮鍵。
聚酰胺和聚酰亞胺結合劑比酚醛樹脂結合劑具有更高的韌性、熱阻和彈性。聚酰亞胺結合劑的韌性是酚醛結合劑的5到10倍,可(kě)以承受300°C的溫度20倍的時間。然而,較高的價格使得這種粘合系統類型的使用(yòng)限制在特殊應用(yòng)和超硬磨料上。聚酰亞胺樹脂是高産量硬質(zhì)合金磨削的主要結合劑類型,特别是用(yòng)于凹槽磨削,或用(yòng)于冷卻潤滑劑下的切割磨削。
1.4 環氧或聚氨酯樹脂
環氧或聚氨酯輪是樹脂粘合輪中最軟的。對于傳統磨料,常用(yòng)于雙盤和外圓磨削。然而,對于超硬磨料,環氧或聚氨酯結合劑似乎僅限于玻璃和陶瓷行業的微米鑽石顆粒應用(yòng)。環氧樹脂的特性是它們的環氧基,由環氧環(–CH2–O–CH2–)組成。然後,環氧樹脂與流體(tǐ)硬化劑硬化為(wèi)聚合物(wù)。
2 樹脂結合劑的制造
樹脂粘合磨具是通過混合、壓制和在約200°C的溫度下硬化制造的(見圖4)。樹脂通常由兩個主要成分(fēn)樹脂和硬化劑組成。混合會産生反應性樹脂材料。在硬化過程中,樹脂的粘度升高,生成一種硬塑性材料。
2.1 混合和成型
混合通常分(fēn)為(wèi)幾個步驟,濕混合、幹混合和最後混合(見圖2)。在濕混合步驟中,磨料顆粒和液體(tǐ)樹脂或糠醛(一種潤濕劑)結合在一起。磨料顆粒将被塗覆,使得樹脂粉和填料更容易附着在顆粒表面。潤濕劑也改善了顆粒的聚集。此外,磨料工具可(kě)以在其原始的,所謂的“綠色”狀态下處理(lǐ)。
在與濕混合物(wù)(由磨料和濕樹脂組成)結合之前,以酚為(wèi)基礎的粉末樹脂和填料進行幹混。添加劑被包含在内,以通過改善混合物(wù)的流動性和儲存壽命,減少團塊傾向來支持混合過程。添加劑的例子包括粉末添加劑、矽石和衍生物(wù)。混合過程繼續進行,直到出現均勻的、可(kě)傾注的混合物(wù)。在處理(lǐ)樹脂粉時,粉塵是一個安(ān)全問題。因此,防塵劑可(kě)以是有用(yòng)的添加劑,以最小(xiǎo)化粉塵。
在壓制之前,可(kě)以嵌入體(tǐ)材料,如用(yòng)于切割輪的玻璃纖維或用(yòng)于超硬磨輪的鋁體(tǐ)。
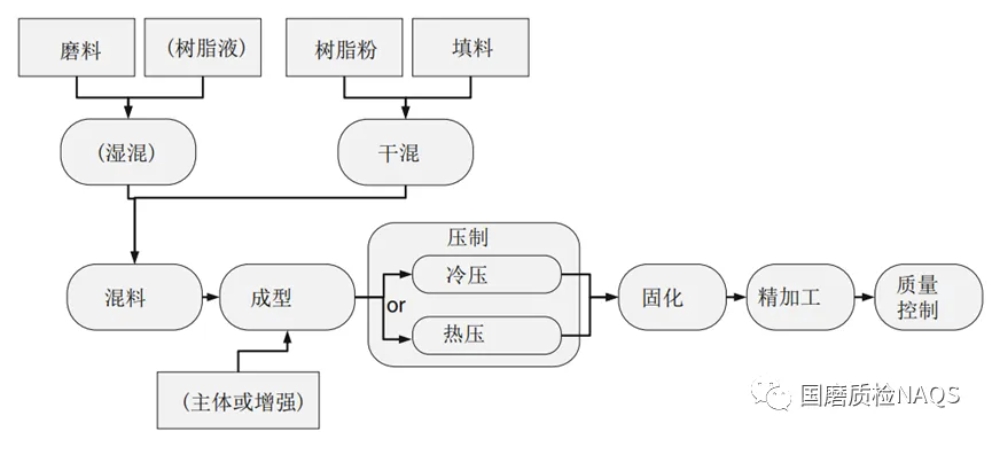
圖2 樹脂砂輪制造過程
2.2 壓制
結合劑和磨料混合物(wù)可(kě)以在爐子中冷壓并硬化,也可(kě)以在帶有加熱闆的壓力機上熱壓并硬化。圖5顯示了将磨料層壓到磨輪體(tǐ)上的壓制示例設置。傳統的砂輪可(kě)以在140-200°C下進行熱壓或冷壓并硬化。大多(duō)數超硬磨輪和密實、低孔隙度的磨輪是通過在160-175°C下進行熱壓制造的。對于直徑小(xiǎo)于200mm的超硬磨輪,可(kě)以直接将磨料層壓到基體(tǐ)上。環氧或聚氨酯結合劑是在模具中鑄造或搖動,然後在20-80°C的溫度下硬化。
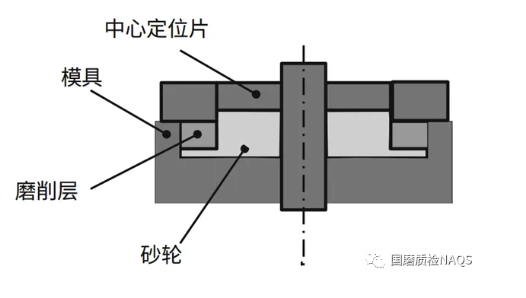
圖5 樹脂砂輪壓制
冷壓是在液壓機上進行的,壓縮強度為(wèi)15-30 N/mm2。壓制時間範圍從5-50秒(miǎo),取決于磨料工具的尺寸和形狀、顆粒大小(xiǎo)、混合物(wù)的塑性和分(fēn)布。在熱壓中,壓制時間為(wèi)每毫米輪厚約30-60s。
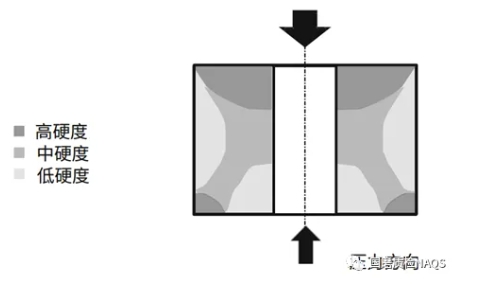
圖6 壓制砂輪的理(lǐ)論硬度偏差示意圖
壓制過程可(kě)以基于定義的體(tǐ)積或壓力進行(定體(tǐ)積和定壓力)。内部摩擦和與模具壁的摩擦導緻顆粒密度的偏差,從而影響工具硬度(見圖6)。密度偏差可(kě)以通過兩個砧壓或在壓制過程中振蕩來克服。
2.3 固化
硬化過程必須遵循定義的溫度程序(見圖7中的示例)。根據實際溫度,固化過程中會發生幾種化學(xué)過程:
(1)70~80°C:樹脂結合劑開始流動,并轉化為(wèi)熔融質(zhì)量。酚醛樹脂中的水蒸發,樹脂在這種水分(fēn)離下硬化。水可(kě)以在多(duō)孔工具中排出。(2)110-120°C:六次甲基四胺分(fēn)解并引發熔融樹脂粉的硬化過程(見圖8)。氣體(tǐ)釋放,特别是氨(NH3)。(3)170-180°C:結構最終硬化,酚醛樹脂的交聯發生。應避免過度固化,因為(wèi)過度固化的工具強度降低。(4)180-200°C:苄胺結構分(fēn)裂,産生新(xīn)的氨生成(見圖8)。樹脂結合劑變得脆性,但也變得熱穩定。(5)最終溫度水平(165-170,175-180,或185-195°C)顯著影響最終工具性能(néng)(硬度、韌性、脆性)。固化也可(kě)以通過射頻和微波加熱的介電(diàn)方式進行。這些方法需要存在顯著的電(diàn)損耗因子,這在酚醛醛樹脂中是常見的。
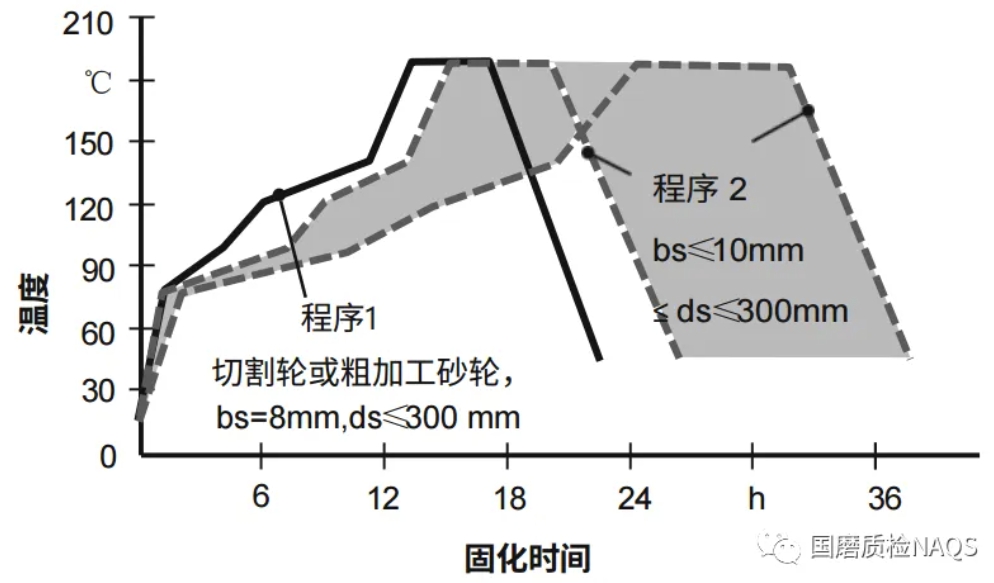
圖7 示例:兩款砂輪——不同寬度(bs)和類似砂輪直徑(ds)條件下,固化溫度曲線(xiàn)示例。
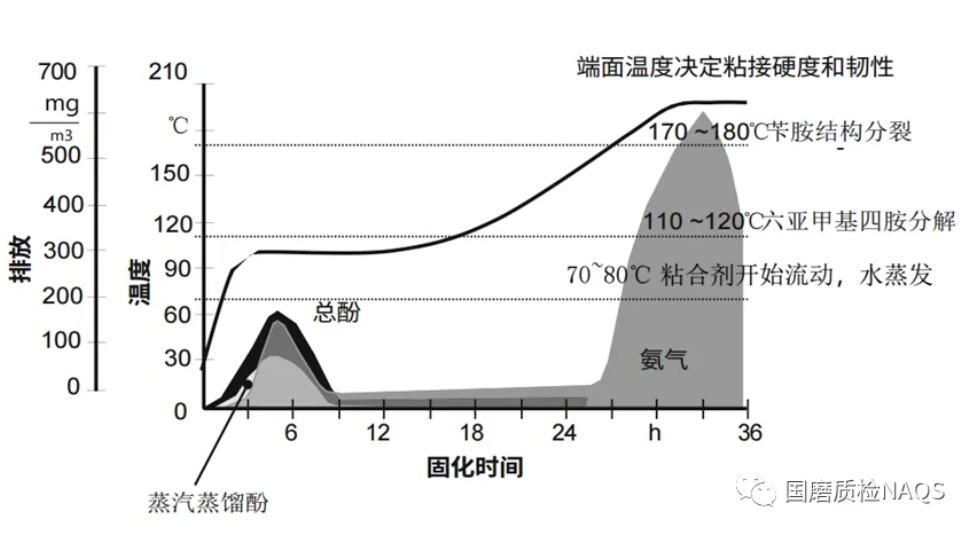
圖8 樹脂結合劑砂輪固化時的溫度曲線(xiàn)和排放物(wù)
2.4 樹脂結合劑中的填料
樹脂結合劑中的填料在制造階段和磨削操作(zuò)中以下作(zuò)用(yòng):引入氣孔,增強結合劑性能(néng),改變外觀,等等。
樹脂粘合磨具中常見的填料有冰晶石-氟化鈉鋁(Na3AlF6)、黃鐵礦(FeS2)、硫化鋅(ZnS)、硫酸鋅鋇(ZnSBaSO4)、氟硼酸鉀和氯化鉀(KAlF4, K3AlF6)、硫酸鉀(K2SO4)和這些材料的混合物(wù)(KCl)。
過去使用(yòng)的有毒材料三硫化二銻(Sb2S3)和氯化鉛(PbCl2)已被特殊的鐵鹵化物(wù)和其他(tā)物(wù)質(zhì)取代。填料和樹脂結合劑的百分(fēn)比随磨具硬度和密度的變化而變化(表1)。
表1 砂輪中常見的樹脂和填料含量百分(fēn)比
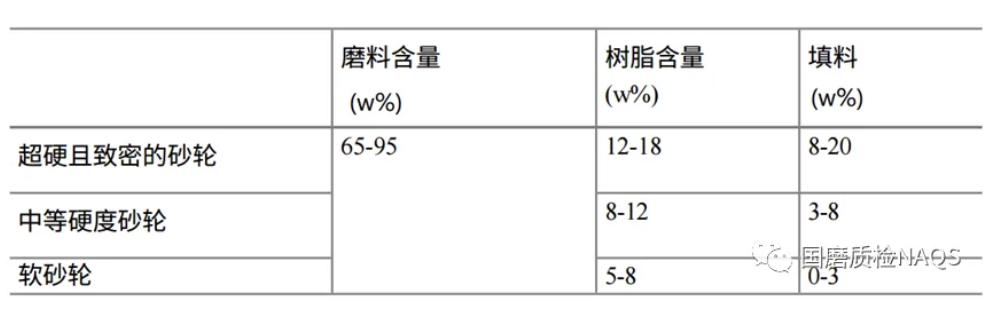
在制造階段,填料可(kě)以引入氣孔。基本氧化物(wù),如CaO和MgO,是加速硬化過程的填料。然而,CaO隻應用(yòng)于幹磨操作(zuò)的磨具,因為(wèi)CaO填料在接觸冷卻潤滑劑時可(kě)以水化并轉化為(wèi)CaCO3。
在磨削過程中,填料增強了結合劑的韌性、耐熱性、強度和爆裂阻力,或者它們作(zuò)為(wèi)次要磨料支持磨削過程。玻璃碎片增強了砂輪的内徑。可(kě)以将具有高熱導率的細金屬粉末引入到結合劑中,以改善工具在加工過程中的熱吸收。如:細銀粉, 325目或更細。此外,細矽酸鹽顆粒作(zuò)為(wèi)結合劑的增強劑。
引入到結合劑配方中的固體(tǐ)潤滑劑形式的填料有以下作(zuò)用(yòng):
• 減少了砂輪/工件界面的摩擦,
• 通過磨削切屑減少了砂輪的負載,
• 保持磨料顆粒的鋒利度。
如:325目或更細的砂輪的有機幹膜潤滑劑聚四氟乙烯(PTFE)類型。在其他(tā)應用(yòng)中,潤滑劑FeS2和K2SO4改善了磨削質(zhì)量和通用(yòng)性。細分(fēn)的石墨可(kě)以改善幹磨的性能(néng)。氟化鈉鋁(Na3AlF6)在約950°C時熔化,防止金屬堵塞砂輪。然而,它作(zuò)為(wèi)Al2O3顆粒的溶劑。将在非常基本的介質(zhì)中使用(yòng)的磨料帶的樹脂結合劑必須進行額外的穩定。當填料作(zuò)為(wèi)着色劑時,填料可(kě)以改變工具的外觀。
3 樹脂結合劑的性能(néng)
樹脂結合劑具有相對較高的彈性。因此,這種結合劑類型被選用(yòng)于受到沖擊、側向負載、突然負載或高切削速度的砂輪。典型的應用(yòng)是切割或粗加工。此外,樹脂結合劑對于完成過程以達到高表面質(zhì)量效果很(hěn)好。然而,結合劑的彈性可(kě)能(néng)對尺寸精(jīng)度産生負面影響。
樹脂粘合輪易于成型,但通過成型不能(néng)達到足夠高的出刃高度。因此,需要額外的銳化過程。表1列出了磨輪中常見的樹脂和填料含量百分(fēn)比。在磨削過程中,隻有使結合劑回退的工件材料才會導緻足夠的自銳化效果。适合的材料是脆性材料,例如在硬質(zhì)合金工具磨削的應用(yòng)中。
密實的磨具表面是通過細磨料顆粒大小(xiǎo)實現的。大顆粒和金屬顆粒鍍層改善了樹脂粘合系統中的結合力。某些填料,如CaO,不應接觸水。
此外,樹脂結合劑對熱敏感。超過200°C的溫度下開始降解,磨料鍍層有助于散發磨削熱。樹脂砂輪的保質(zhì)期有限,應在兩年内使用(yòng)。使結合劑樹脂硬化的聚縮反應不會導緻完全硬化,因此樹脂結合劑的強度可(kě)能(néng)會因為(wèi)大氣或化學(xué)暴露而改變。
以上内容轉載自:國(guó)磨質(zhì)檢NAQS。